PUMP OPTIONAL EQUIPMENT
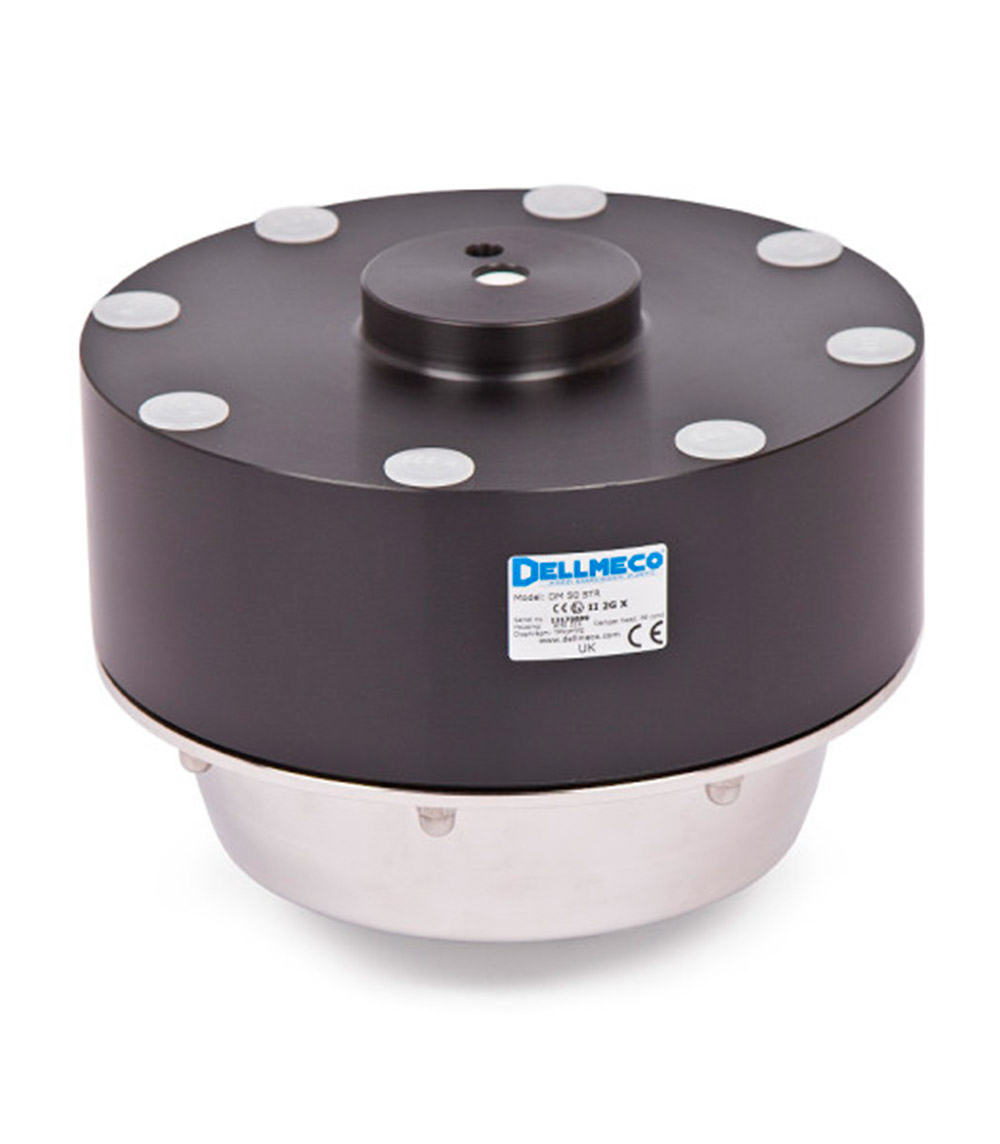
OPTIONS
- Diaphragm materials: EPDM, NBR, PTFE/(TFM) / EPDM, PFA/PTFE/(TFM) / EPDM,
- high resistance to abrasives/corrosives
- excellent torsion and restoration properties
- designed for wide range of temperatures
- easily removed during maintenance
- Ball valves in EPDM, NBR, PTFE, PU (polyurethane) ceramics or AISI 316
- Cylinder valves in PE or PTFE (for Plastic pump series only)
- Air valves in PETP with FPM or NBR seals, brass with FPM or EPDM seals, AISI 316L with FPM seals
- Solenoid valves (MV option) for precise and constant dosing applications
- High pressure (HPM or HPS) options available (for up to 16bar)
- Barrier chamber (BC1, BC2, BC3) options for optimum control of media
- Diaphragm monitoring (DM1 or DM2) available
- Wide range of stroke sensor and counting (SC) options
- Back flushing (hand-operated or pneumatic operated)
- Cleaning-in-Place (CIP), Sterilise-in-Place (SIP) for Hygienic Pumps
- Pulsation dampener (on suction and/or discharge ports and also as an integrated option)
- Drum pump and pneumixer options + attachments
- Various flange connections to meet specific customer requirements
- DIN PN 10
- PN 10 DIN 2576
- PN 10/16 DIN 2277/2278
- AISI 150 RF-SO
- JIS B2220
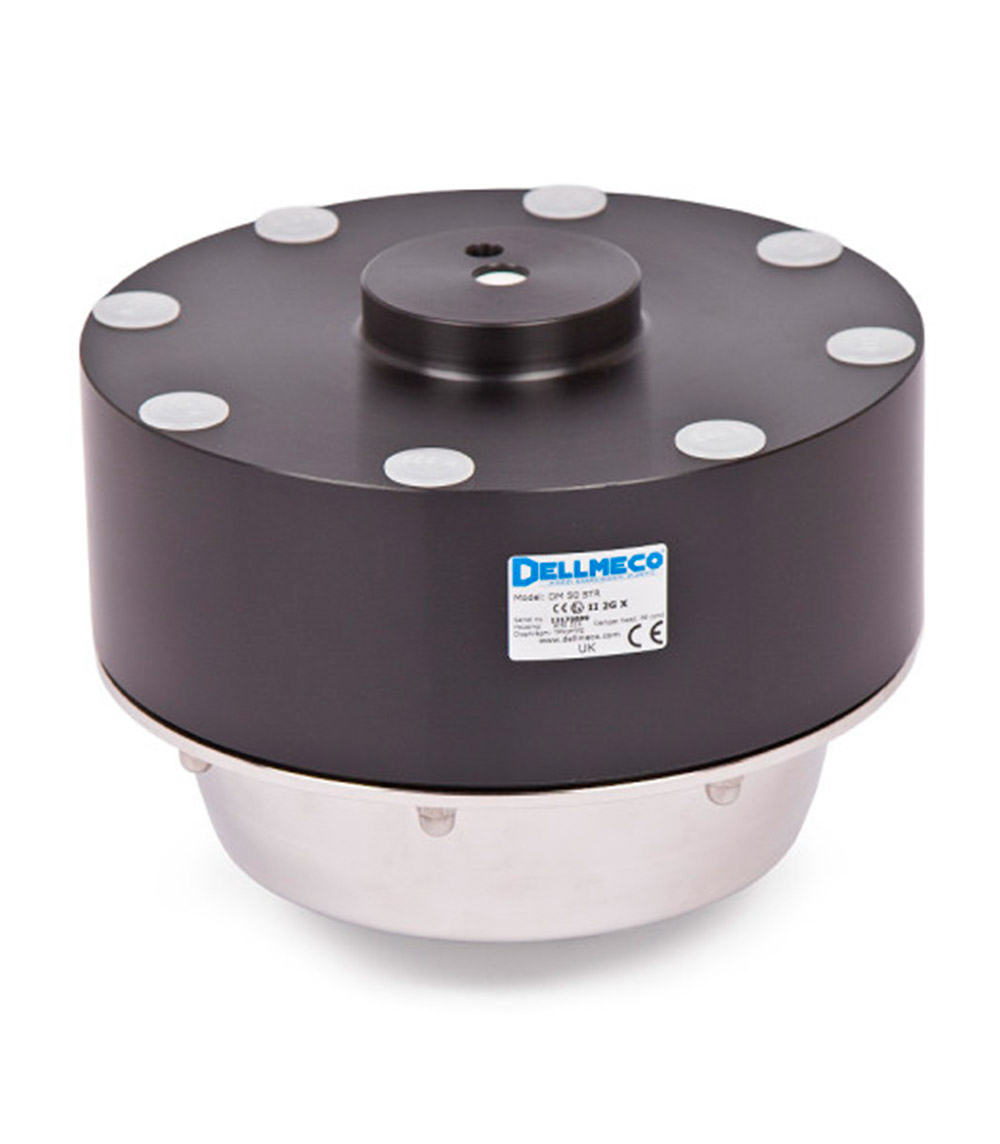
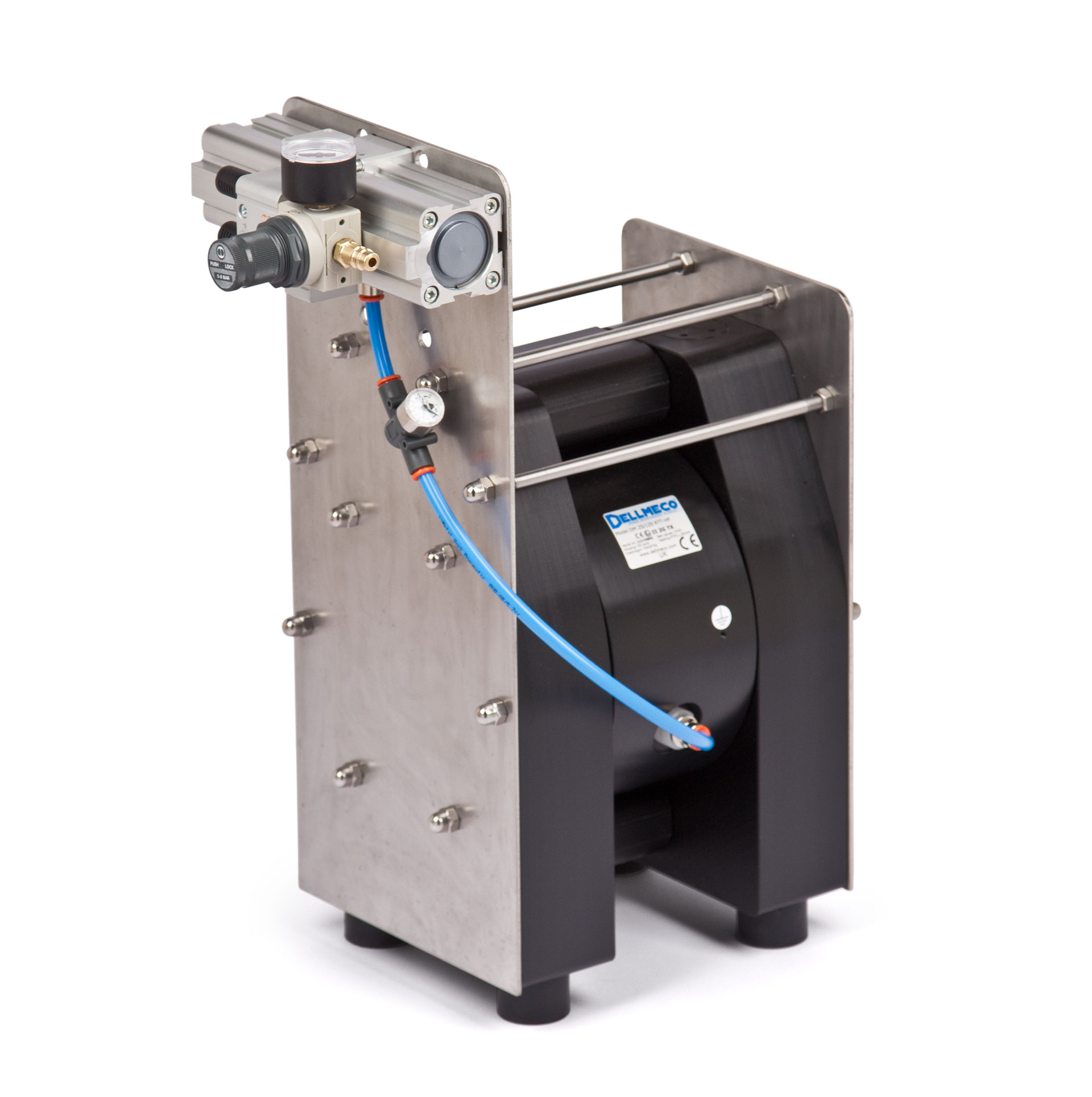
High pressure plastic pump with booster (HP option)
The high pressure (HP) option is a compact booster that can be directly mounted to the pump. It is capable of doubling the delivery pressure and, for example, with an available air pressure of 7 bar the pressure can be up to 14 bar.
The design is based upon the standard DELLMECO pump made from machined polyethylene (PE). A pressure regulator is already incorporated with the unit for easy adjustment.
Applications include filter presses and slurry drying especially in the food and beverage industry as well as for water and wastewater management.
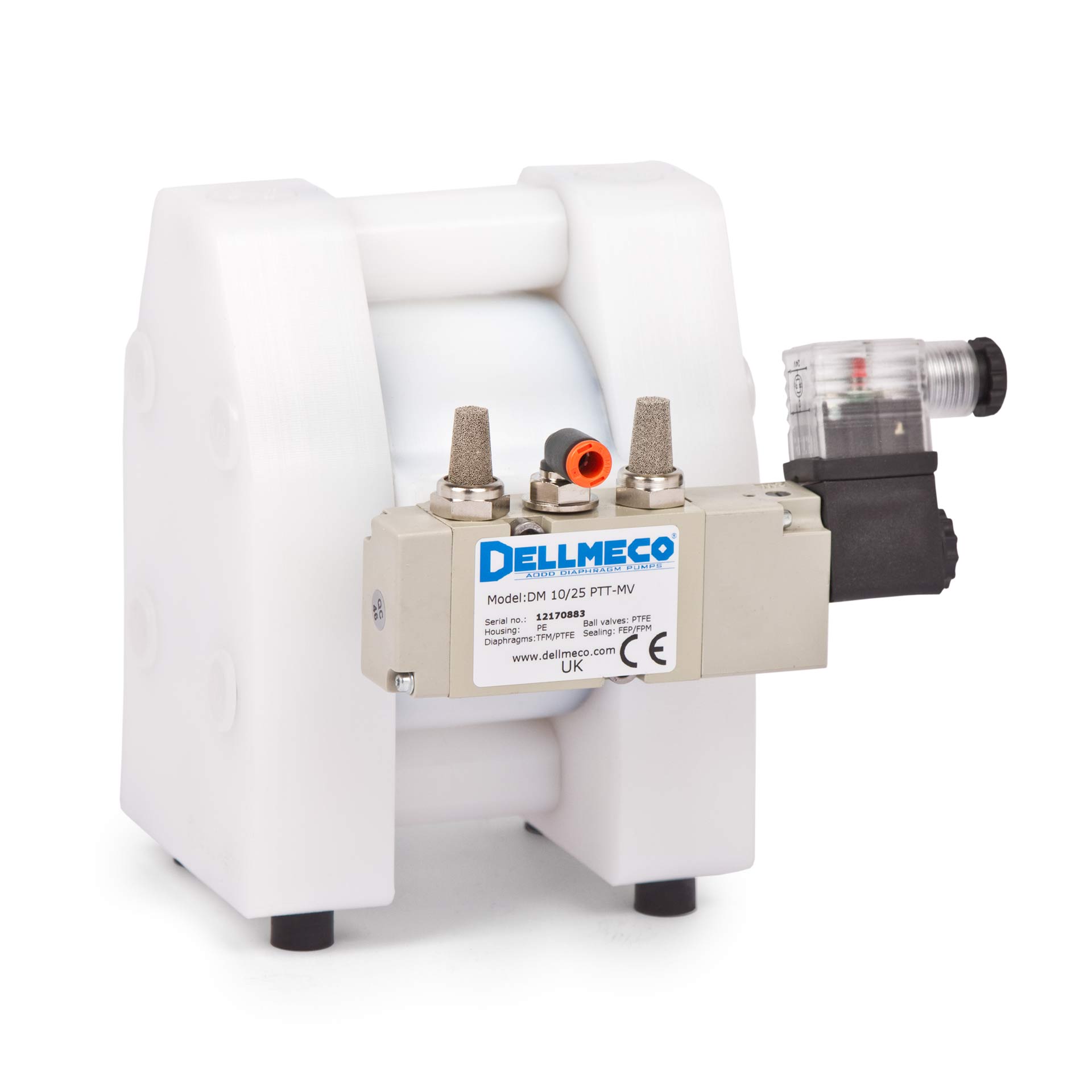
Plastic pump with solenoid valve (MV option)
DELLMECO plastic pumps with the MV option replace the standard air valve with a solenoid air valve. This enables media to be delivered in precise and constant volumes for such applications as found in the chemical industry.
The pump is fitted to a 2-position, 4-way solenoid valve. When the solenoid is unpowered, one chamber within the pump is pressurised with air, whilst the opposite chamber is discharged. When electric power is applied, the solenoid re-pressurises the discharged chamber and the opposite chamber is then discharged.
By alternatively turned on and off, the solenoid enables the unit to run like a standard DELLMECO pump and no lubrication is needed.
This option requires 24 V DC to operate.
Pumps with the MV option are non-submersible.
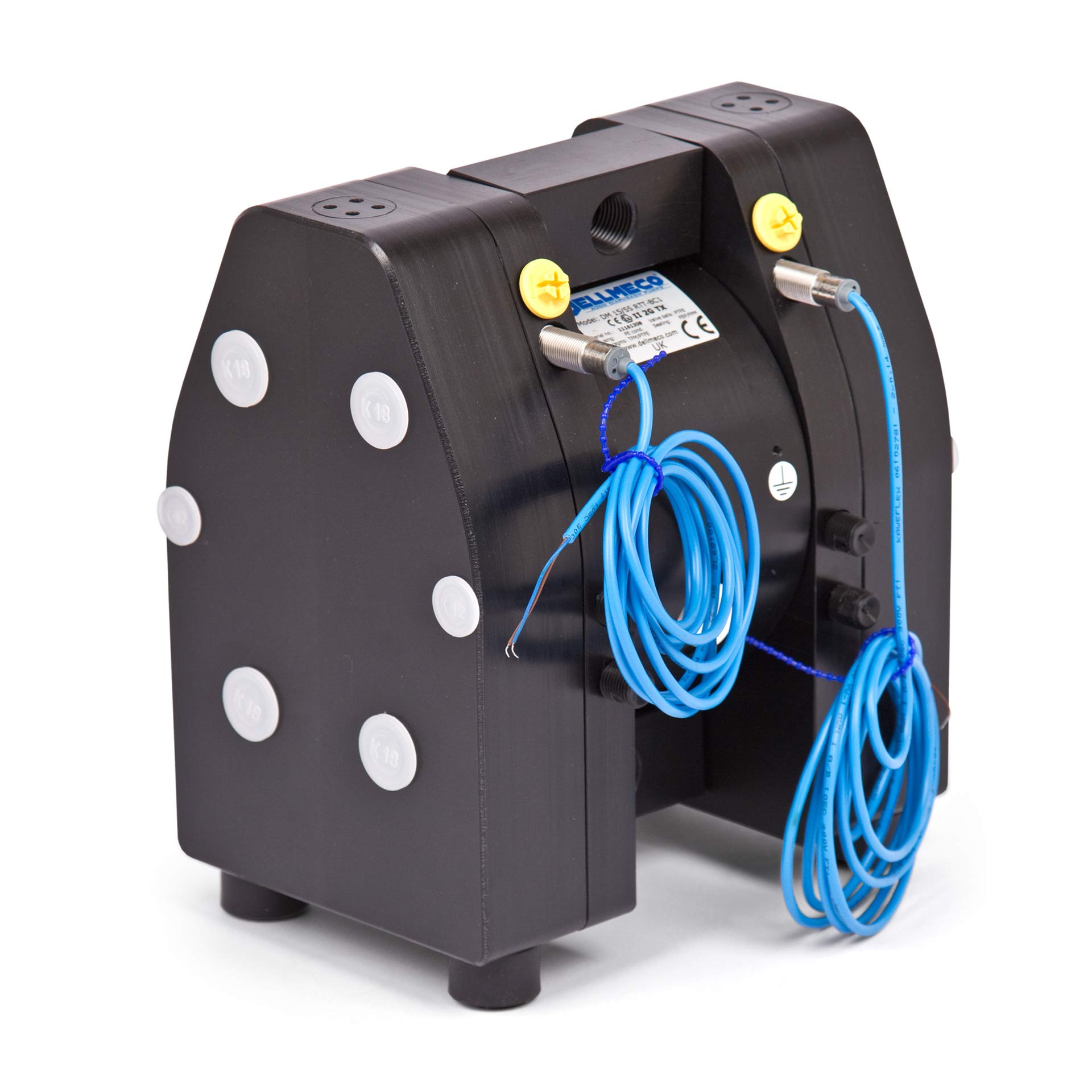
Barrier chamber system (BC option)
The comply with increased safety standards, this system replaces the standard diaphragm by a tandem arrangement of two diaphragms and a PE conductive barrier chamber filled with a non-conductive liquid (usually de-ionised water).
Sensors monitor the conductivity of this liquid and if the diaphragm fails, they detect the change in conductivity and an electronic signal is sent to a controller.
The barrier system is available with three options:
BC1 – barrier system with sensors, standard
BC2 – barrier system complete with sensors and controllers
BC3 – barrier system complete with sensor and controllers for expolosion-prood zones – ATEX
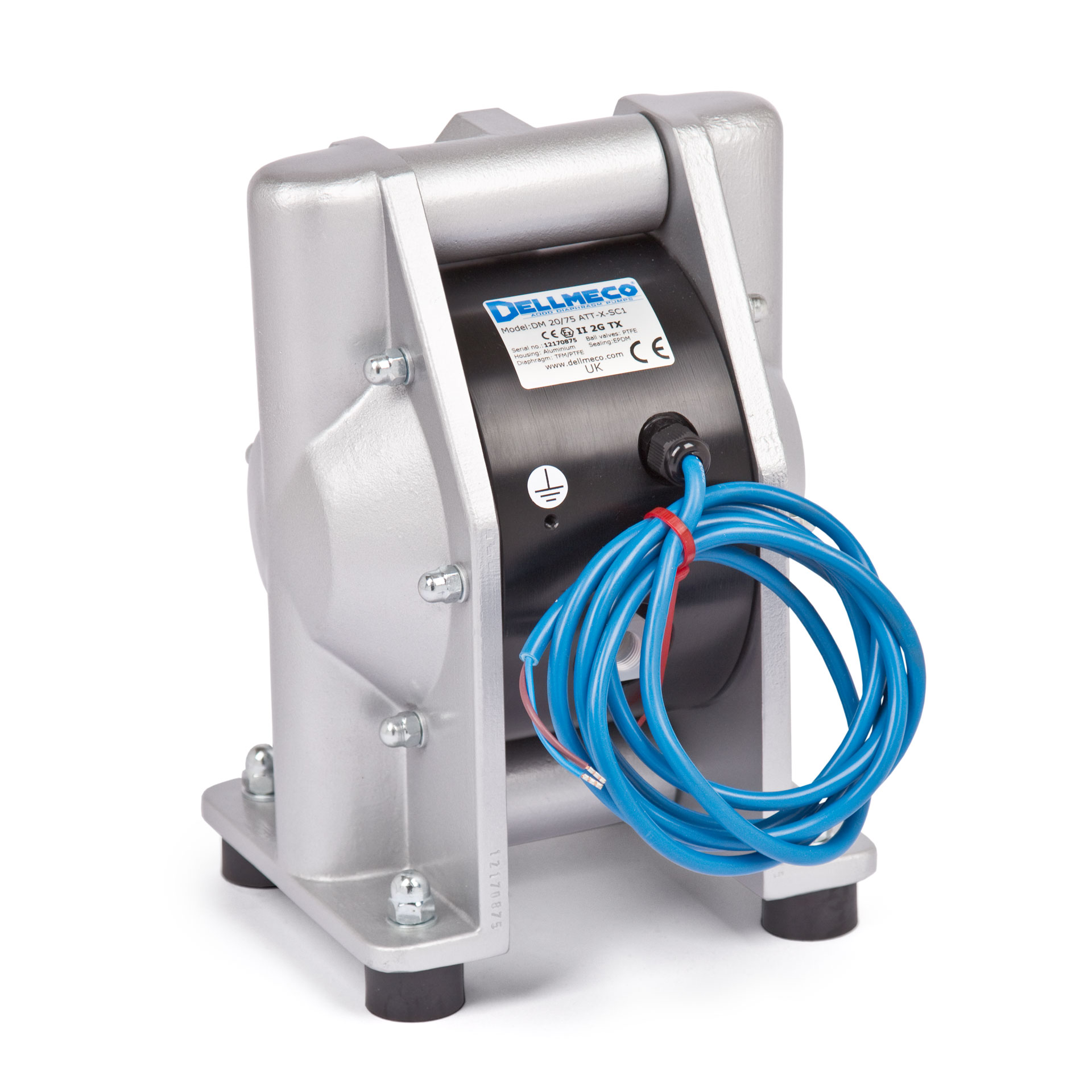
Stroke counting (SC options)
A sensor is installed in the central pump housing to count the strokes. The diaphragm is scanned without physical contact by this sensor – ensuring safe monitoring totally independent of external influences and the pump’s mode of operation. The signal from the sensor is sent as output data to either existing detectors or to a digital counter (also supplied). When the pre-set value is reached the stroke counter can be shut down with, for example, a solenoid valve.
The stroke counting system is available in five options:
SC1 – Stroke sensor (NAMUR type) also for explosion-proof zones
SC2 – Stroke counting system complete with sensor and counter
SC3 – Stroke counting system complete with sensor, counter and controller for explosion-proof zones
SC4 – Pneumatic stroke counting system with pressure transmitter
SC5 – Pneumatic stroke counting system with pressure transmitter and counter
In cases where only the sensor id required (code SC1), it has to be connected to an existing controller with a Namur type inlet. For explosion-proof applications, the stroke counting option requires an intrinsically safe controller (code SC3), which had to be installed between the sensor and counter. The wiring diaphragm and technical data is supplied with the electric units. The controllers have to be installed an a suitalbe cabinet.
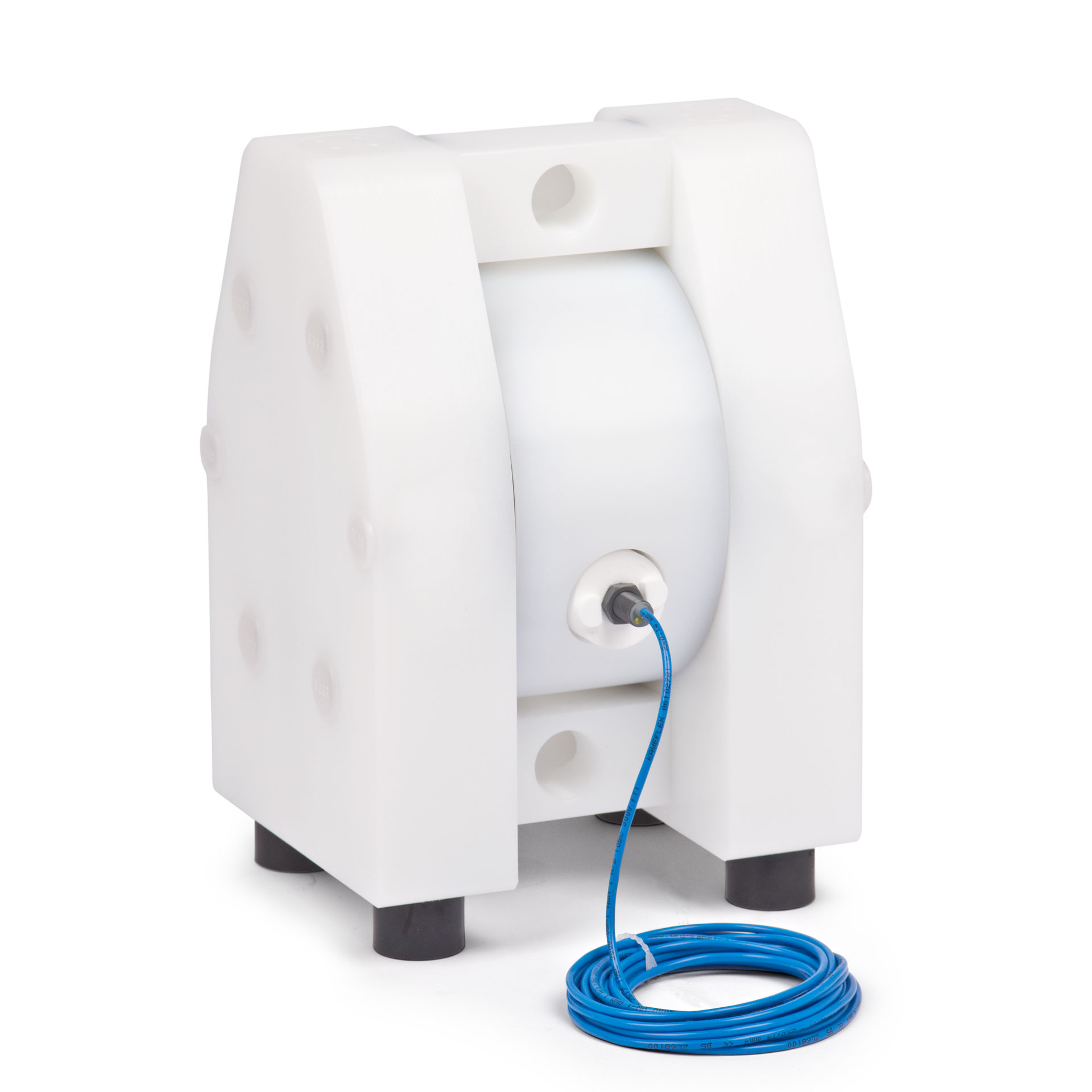
Diaphragm monitoring (DM options)
Although DELLMECO diaphragms are designed for optimum service and maximum lifespan, regular maintenance must be included as part of the service programme. This is called ‘preventive maintenance planning’ (PMP). However, for increased security in sensitive applications, any pump failure from, for example, the media leaking into the pump central housing can be simply and effectively prevented by installing a DELLMECO diaphragm monitoring system.
A capacitive diaphragm sensor is mounted in the pump muffler which monitors any media in proximity to the sensor. Thus, immediate remedial actions can by taken.
The diaphragm monitoring system is available in two options:
DM1 – Diaphragm sensor (NAMUR type) also for explosion-proof zones
DM2 – Diaphragm monitoring system complete with sensor and controller (S)
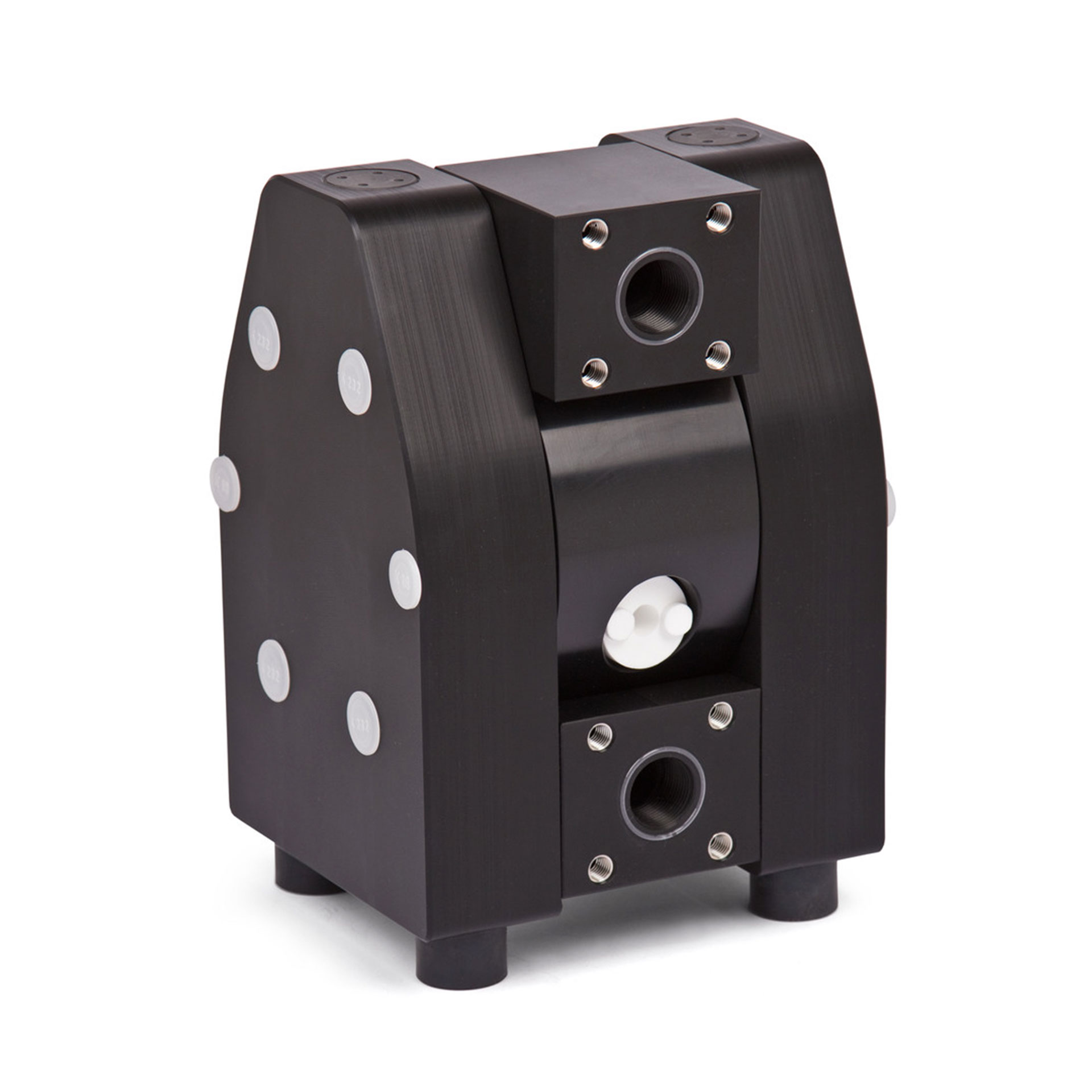
Flange connections (PN10 options)
This option offers the possibility to use flange connectors according to DIN/PN10. The inlet/outlet flange connections are by thread bushings made of stainless steel. The attached O-rings have to be inserted into the grooves of the manifolds to improve sealing before connecting the pump.
F1 – Flanfe connection PN 10 EPDM
F2 – Flange connecton PN 10 NBR
F3 – Flange connection PN 10 FEP/FPM
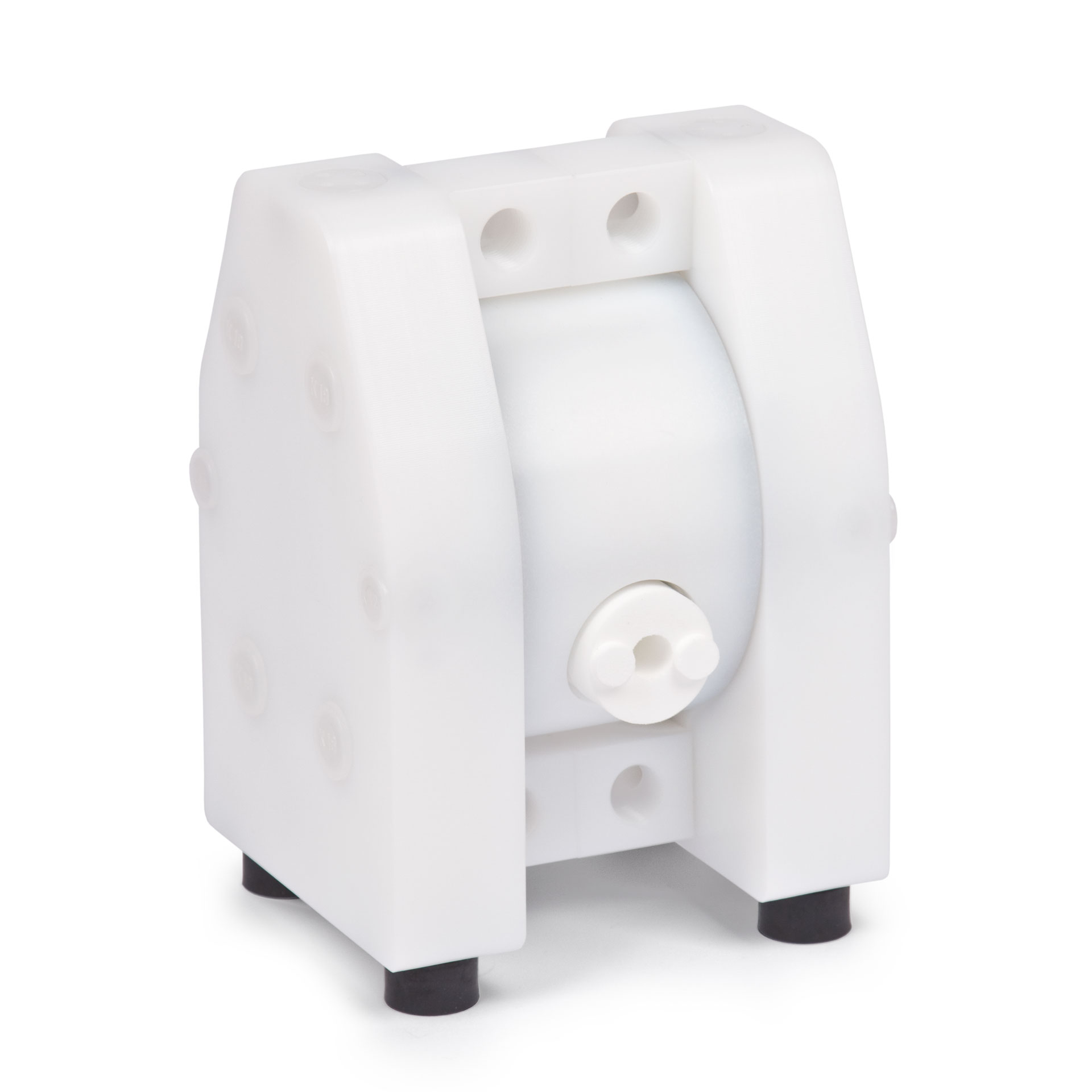
Split connections (S options)
All pump models can be fitted with split connections (code S).
The pump can be converted from a standard double-action air-driven diaphragm pump into a unit with two single chambers. The suction and discharge connection are replaced by a split sleeve with a separate suction and discharge for both chambers. Both chambers are independent and by having them with the same drive it means there can be two media streams in a 1:1 ratio.
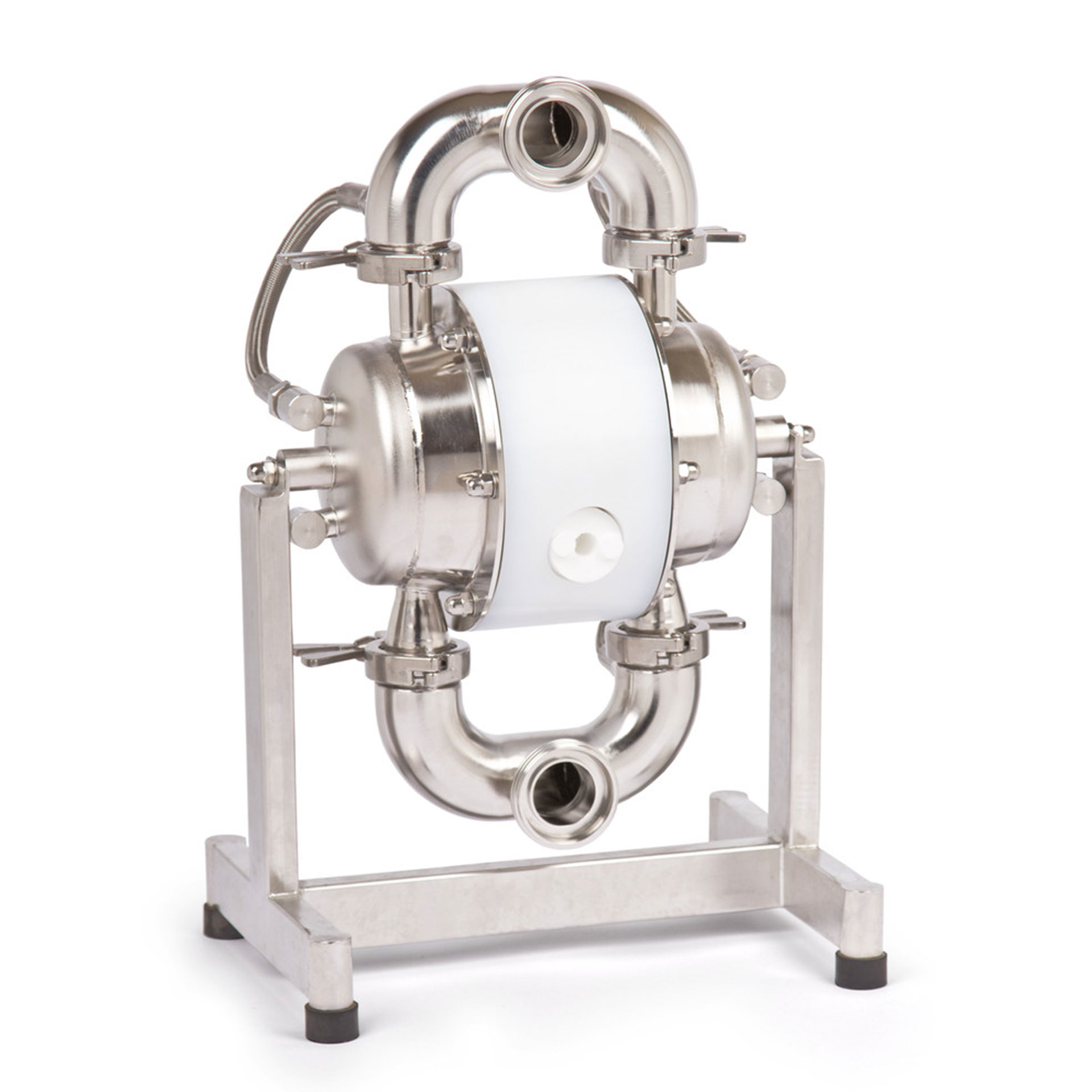
Heating/cooling jacket (HJ options)
The heating/cooling jacket is used when the pumped media has to maintain a specific high or low temperature, throughout the pumping process. A heating or cooling medium is continuously circulated and the jacket also covers all the wetted parts of the pump. This option is available for all our hygienic pump series.
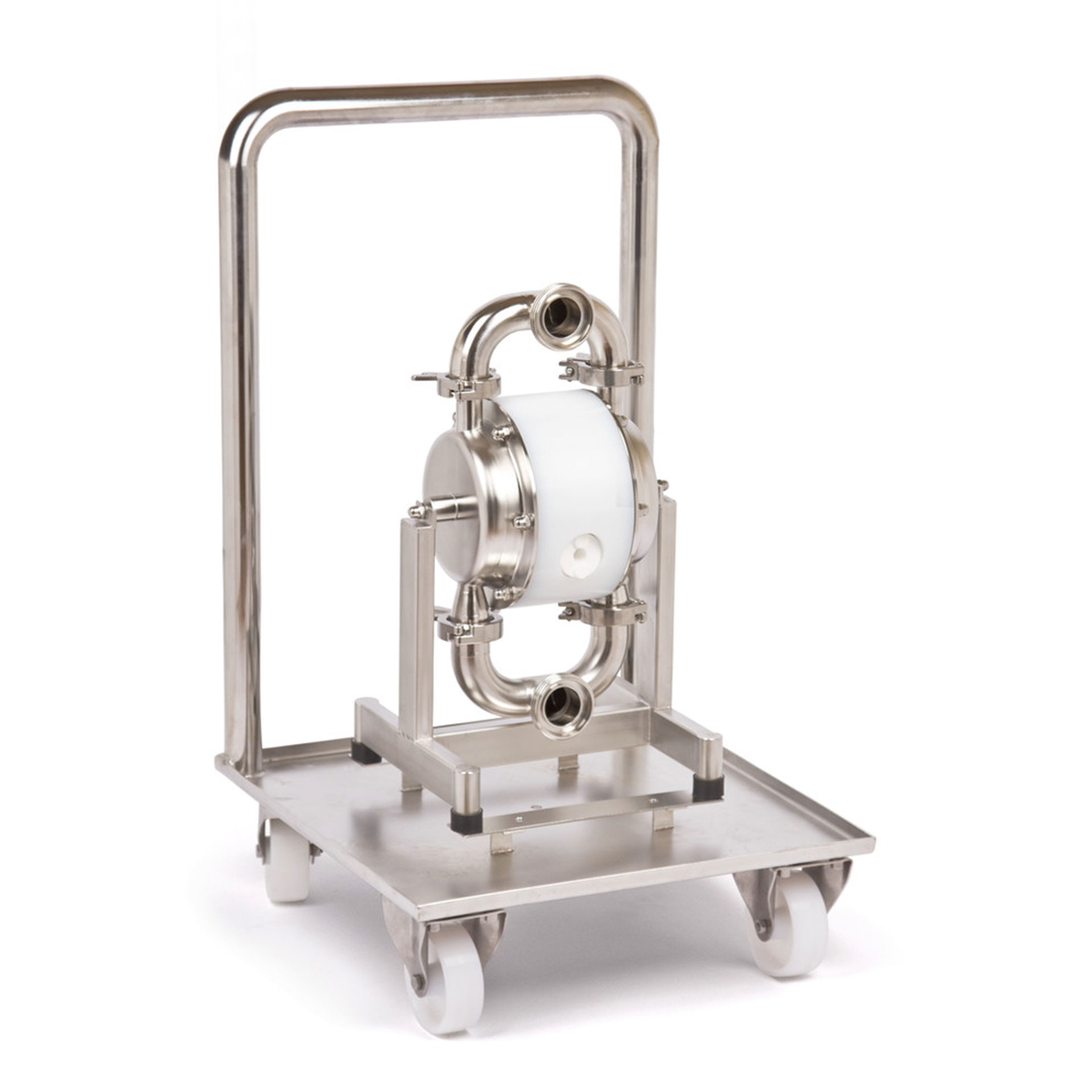
Pump trolley (T options)
Make your DELLMECO pump mobile. The trolley option is available for all pump sizes.
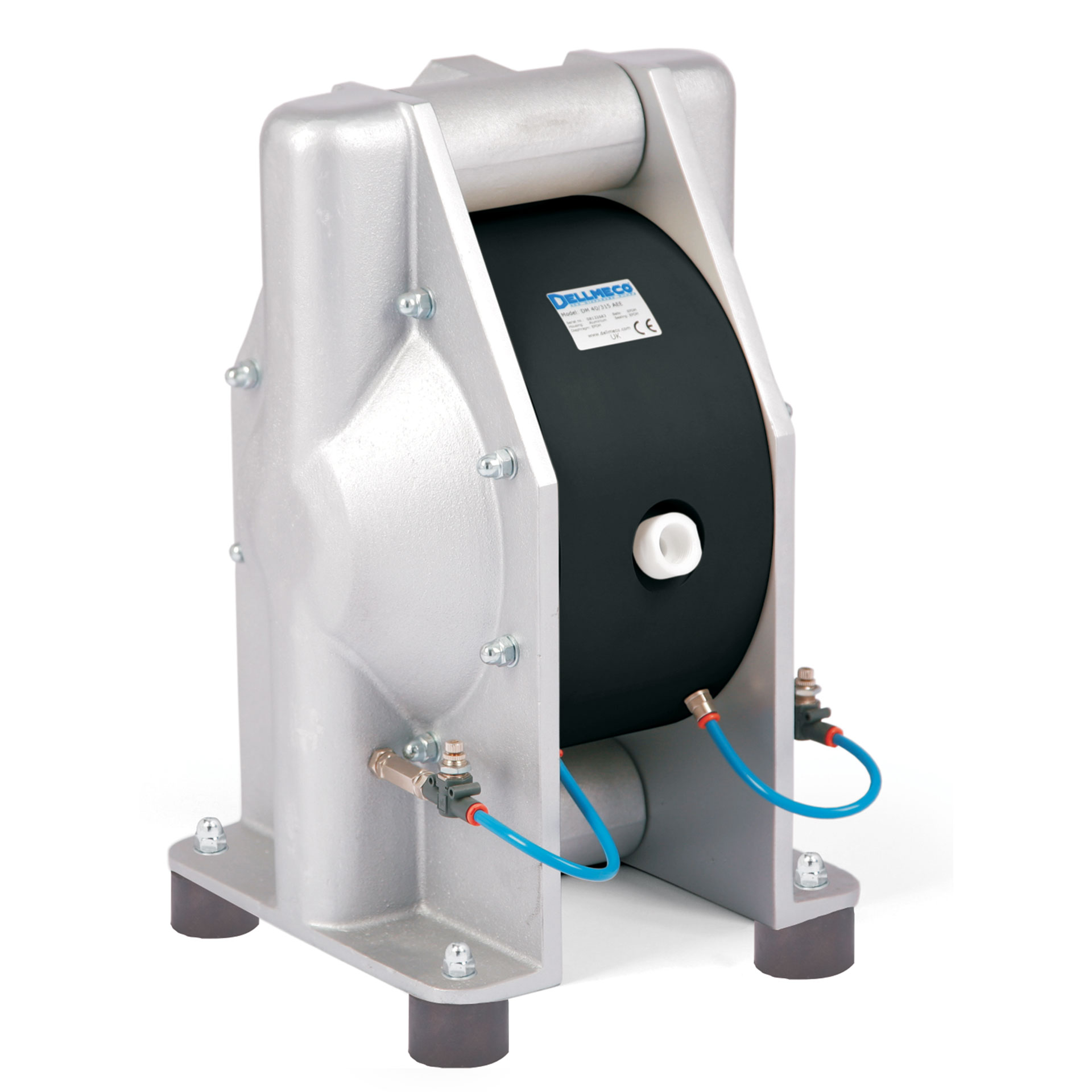
Powder pumps (P options)
DELLMECO pumps can also be used to transfer dry powders more quickly, cleanly and at a praction od the cost than many other systems.
Key features:
– replaces manual powder transfer processes
– reduces airborne contamination – transfers powders directly and in a closed system
– economical and simple – the opposite of large, complex system
– portable – can be moved from site to site
Applications for transferring powders up to 800 kg/m3 (50lb/ft3).
A reliable, efficient and trouble-free transfer of powders including:
– various types of dries food
– limestone
– pharmaceuticals
– talcum
– expanded mica
– silicones and silicas
– carbon black
– acrylic resins
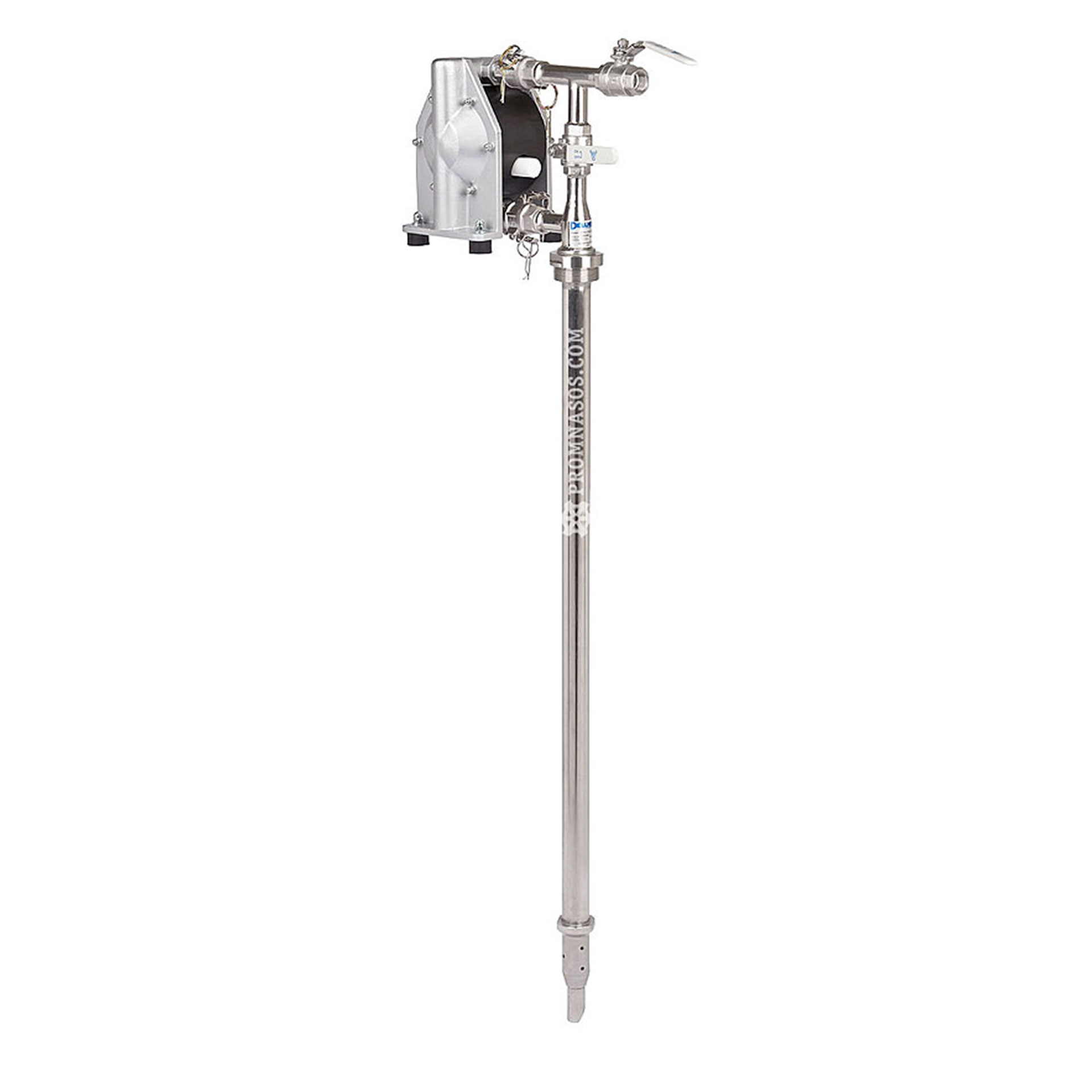
Pneumixers
The Pneumixer works both as a pump and as a mixer. It uses the container to both mix and transfer the media and it fits securely yet simply into the hole used for filling. With this ingenious system there is no need for rolling, shaking or pumping to mix the media. Valuable time and costs are thus saved whilst waste and mess are avoided.
Available in stainless steel AISI 316L (or PP for Plastic Pumps, without ATEX).
Mixing mode
The discharge valve is closed and the re circulation valve opened to allow the media to mix in the container.
Transfer mode
To both mix and pump the media out of the container the discharge valve is opened and the re-circulation valve partially opened.
The length od pipe can be ordered to fit any container size.
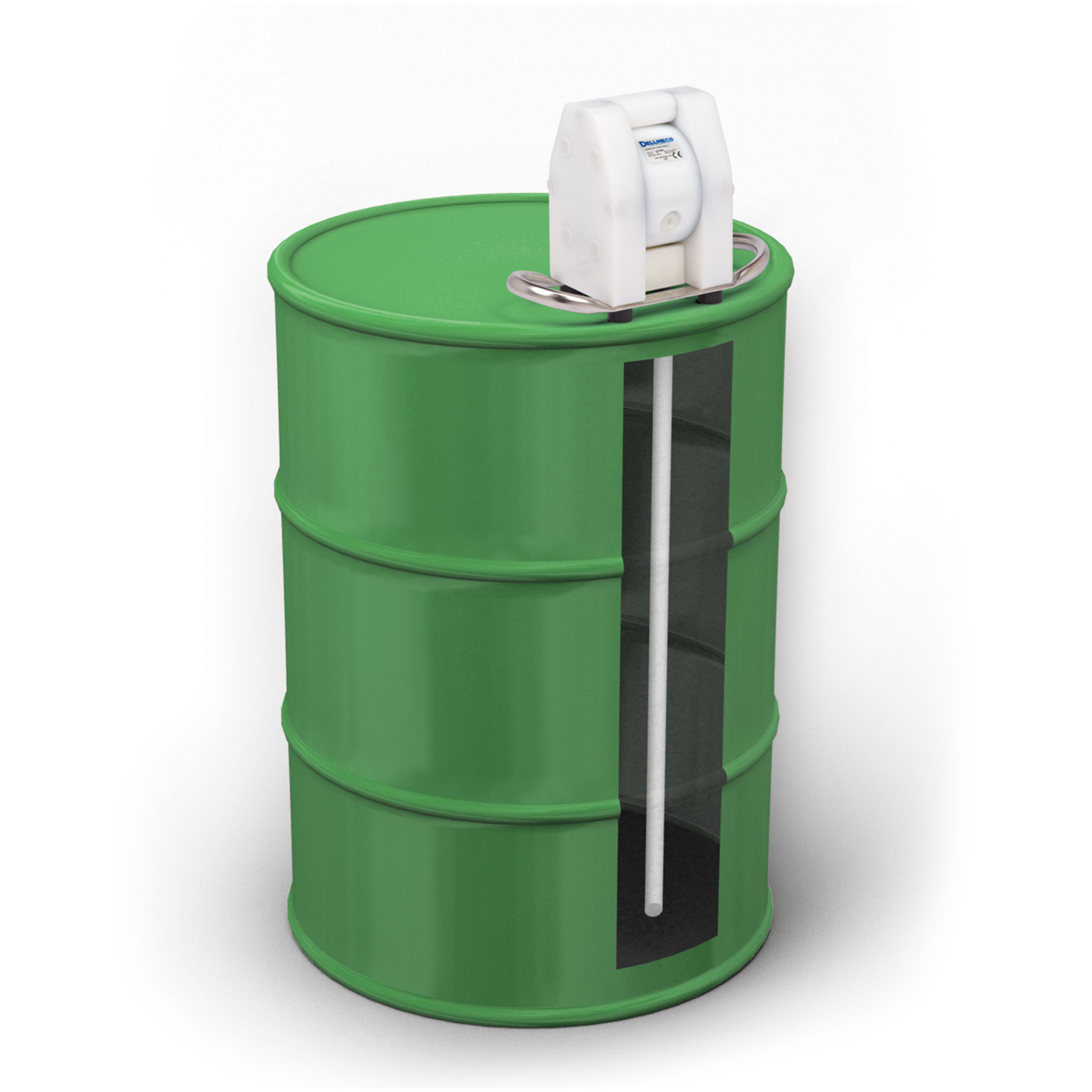
Drum pumps (D options)
DELLMECO drum pumps are available in both standard and conductive PE, PTFE, aluminium and AISI 316L for optimum media compatibility.
The sizes range up to 1″ and they can work with media of different viscosities.
Converting 3/8″, 1/2″, 3/4″ or 1″ plastic or metal pumps to a drum or real application is easy. The adaptor kits are constructed of chemically resistant materials to handle any job. And the drum pipe assembly also comes complete with all the hardware needed. Simply attach the adaptor to the drum and then fix the pump with the pipe connected into the drum.
The standard length of drum pipe is 1.0 , or 1.2 m, but orders can be made to fit any container size.